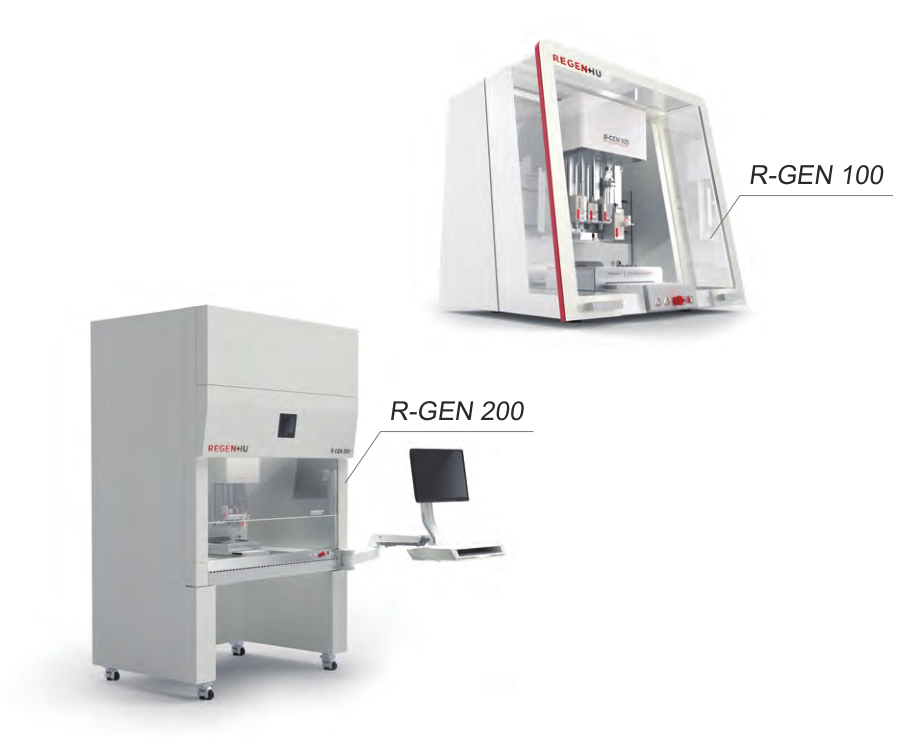
Multiple Technology Combinations |
6 printing technologies available, including microvalve, extrusion, melt extrusion, volumetric dispensing, melt electrowriting, and electrospinning. Multiple technologies help you construct the complicated 3D structure with multiple materials.
|
Modular Design |
5 individual printer head with more than 10 types of accessory, including process supervision system, process observationunit, substrate height calibration unit, light curing kit, etc.
|
User-friendly Software
|
SHAPER software is user-friendly, intuitiveto use, and provides a full set of design tools and process planning management tools. Accomplish all the settings for printings by just THREE steps. Able to receive all updates/upgrades/bugfixes/patches for SHAPER online
|
Integrated Class II Biosafety Enclosure (R-GEN 200 Only) |
Build-in anti-vibration systems Build-in ultraviolet germicidal lamp Configurable mechanical fixation of display panel Type A2 and NSF/ANSI 49 CE conformity
|
Support
|
Hotline support for R-GEN series instruments and software (e-mail, phone, remote support) Service team in China Mainland with rapid and efficient response.
|
Tech Specs
|
Size and weight 770 × 720 × 760mm / 160 kg (R-GEN 100) 1366 × 963 ×2202 mm / 600 kg (R-GEN 200) Build volume: 130 × 90 × 65 mm (Maximal build height depends on the instrument configuration) Minimal dispensing volume: 5 nL Software: SHAPER Workzone temperature: 4~80℃
|
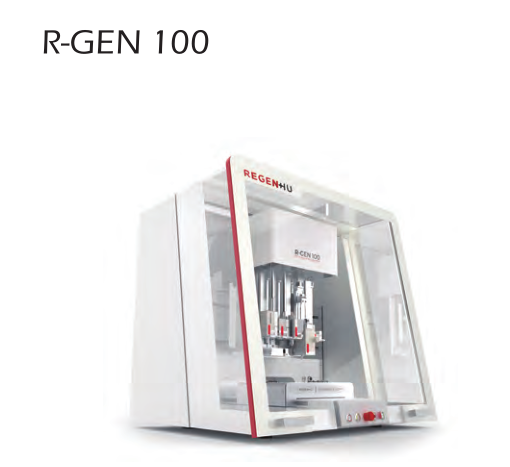

R-GEN Printhead
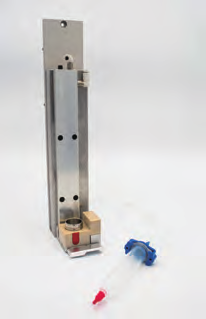 | Pneumatic Strand Dispenser Print scaffolds or continuous strands of medium to high viscous materials.
Materials Hydrogels, pastes, particle suspensions(ceramic or metallic), resins, silicones and many more. Viscosity range: 50-200.000 mPa*s. | 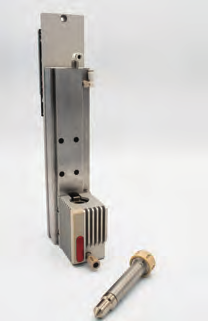 | Pneumatic Melt Dispenser
Build 3D structures from thermoplastics with melting point up to 250°C.Print continuous strands of medium to high viscous materials.Thermoplastic melt electrowriting in conjunction with Electrospinning and -Writing Kit (ESK).
Materials
Thermoplastics, composite pellets or powders, resins, pastes, hydrogels with viscosities up to 200,000 mPa*s.
|
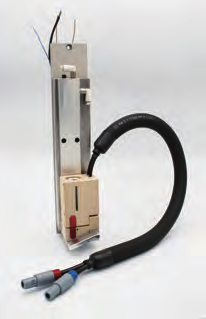 | Pneumatic Drop Dispenser
Jetting cell-laden droplets with controlled volume (down to 10 nL). Deposition of strands of low to medium viscosity materials (up to 1000 mPa*s).
Materials Cell-laden hydrogel precursors (specific nozzle design to maximize cell viability post-printing). Culture media, bioactives, pharmaceutical compounds, and liquids. | 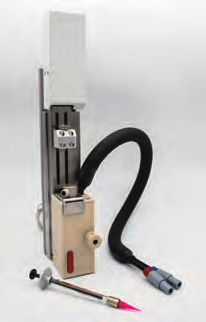 | Volumetric Strand Dispenser
Controlled deposition of materials withcomplex, unpredictable viscosity behavior.Precise volumetric dispensing with 5 nL accuracy. Solution and hydrogel electrospinning in conjunction with Electrospinning and -Writing Kit (ESK).
Materials
Non-homogeneous fluids, hydrogels, pastes, or particle solutions with viscosities up to 5000 mPa*s |
R-GEN Accessories
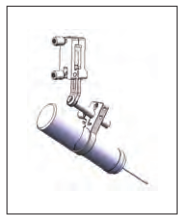 | 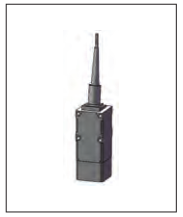 | 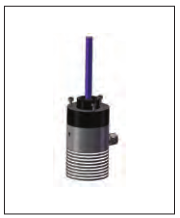 | 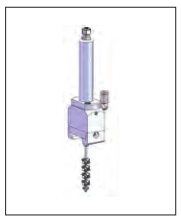 |
Process Observation Unit
Additional unit for real-time monitoring of bioprinting processes.
|
Substrate Height Calibration Unit
System for substrate height detection for precise 3D construction on varying substrates.
|
Light Curing Kit
Select up to 2 distinct wavelengths for ideal photo initiator activation.
|
Cell Agitator
Prevents cell sedimentation and assures cell and particle homogeneity during printing process.
|
Commercial Applications
denovoSkin is a novel commercial solution developed by Swiss company, Cutiss AG, for human skin customization. Through regenHU 3D bioprinter, Cutiss AG is able to bio-engineer large quantities of skin grafts starting off from a very small piece of healthy patient skin. Because of its intrinsic characteristics, denovoSkin is expected to result in a minimally scarring outcome after transplantation. denovoSkin has received a Swissmedic, EMA and FDA Orphan drug designation for the treatment of burns.
Manually | 3D printing |
 | 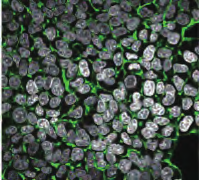 |
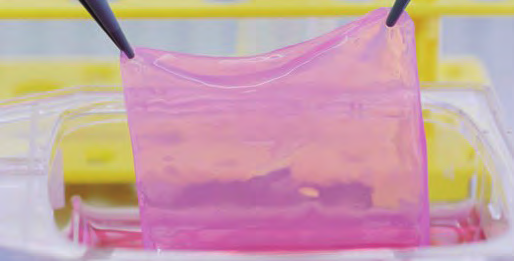
denovoSkin Product
Standard treatment | Use denovoSkin |
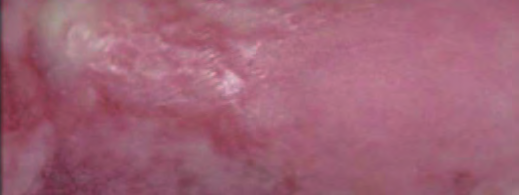 |
Applicationsfor Researches
Organ and tissue customization1
Material researches2
Vascular structure design3
Cartilage printing4
Controlled release tablet5, 6
Drug screening7
Cell scaffold by electrospinning8
[1] Noor et al. Advanced Science. 2019.PMID: 29432987
[2] Kokkinis et al. Advanced Materials.2018. PMID: 29337394
[3] Daly et al. Biomaterials 162. 2018,34-46 PMID: 29432987
[4] Mancini et al. Tissue Eng Part CMethods. 2017; 23, 804-814
[5] Charbe et al. Int J Pharm Investig.2017. 7, 47-59 PMID: 28929046
[6] Khaled et al. Int J Pharm 538. 2018.PMID 29353082
[7] Laternser et al. SLAS Technol. 2018.PMID: 29895208
[8] Ruijter et al. Adv Healthc Mater. 2019.PMID: 29911317
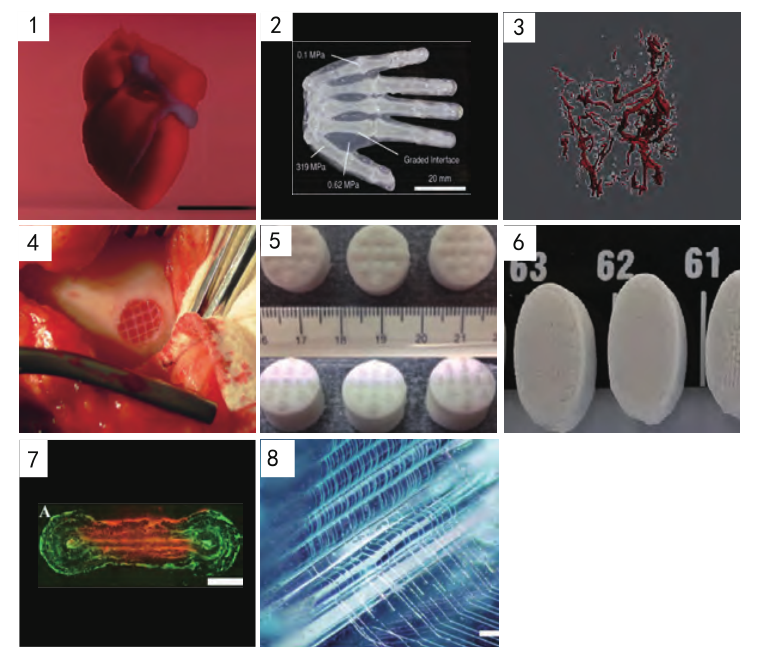
Software (SHAPER)
?
Planning software for 2D/3D design and biofabrication process management for people evolving medicine.
Define and manage your process in 3 simple steps.
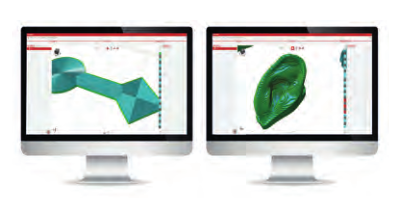
|
Step 1: Designer Use our powerful tools to easily design your 2D or 3D constructs, or import them from another source, define and select multiple printing technologies, and set parameters for the use of various biomaterials, in a single view.
|
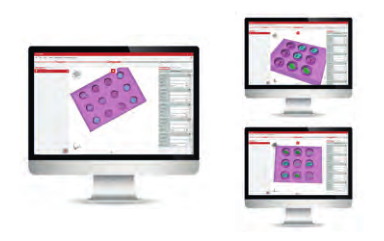
|
Step 2: Composer Improve your printing process definition, compose your print project by positioning your constructs precisely where needed on the print workzone, and define the printing material dispensing order.
|

|
Step 3: Sequencer Quickly visualize and define the planned sequence of your print project, by defining the order, time frequency and parameters of each printing step, simplifying and reducing the time to design your experiment.
|
Applications for Researches
Organ and tissue customization1
Material researches2
Vascular structure design3
Cartilage printing4
Controlled release tablet5, 6
Drug screening7
Cell scaffold by electrospinning8
[1] Noor et al. Advanced Science. 2019.PMID: 29432987
[2] Kokkinis et al. Advanced Materials.2018. PMID: 29337394
[3] Daly et al. Biomaterials 162. 2018,34-46 PMID: 29432987
[4] Mancini et al. Tissue Eng Part CMethods. 2017; 23, 804-814
[5] Charbe et al. Int J Pharm Investig.2017. 7, 47-59 PMID: 28929046
[6] Khaled et al. Int J Pharm 538. 2018.PMID 29353082
[7] Laternser et al. SLAS Technol. 2018.PMID: 29895208
[8] Ruijter et al. Adv Healthc Mater. 2019.PMID: 29911317
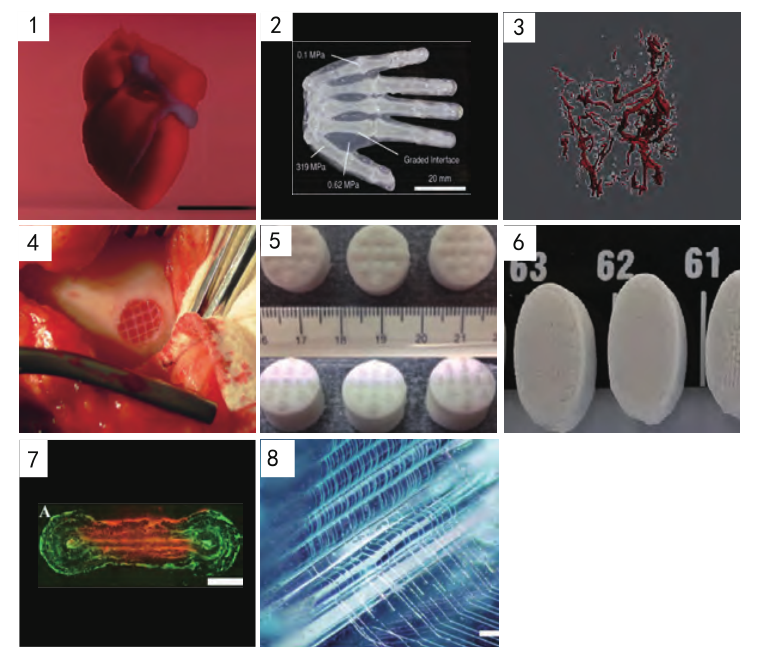
Size and weight
770 × 720 × 760mm / 160 kg (R-GEN 100)
1366 × 963 ×2202 mm / 600 kg (R-GEN 200)
Build volume: 130 × 90 × 65 mm (Maximal build height depends on the instrument configuration)
Minimal dispensing volume: 5 nL
Software: SHAPER
Workzone temperature: 4~80℃